Stainless steel is one of the most popular materials when it comes to welding. It is both durable and possesses high resistance to corrosion, making it attractive for usage in various projects.
However, the material does come with its ups and downs and a welder needs to have enough knowledge about it in order to manipulate stainless steel the proper way.
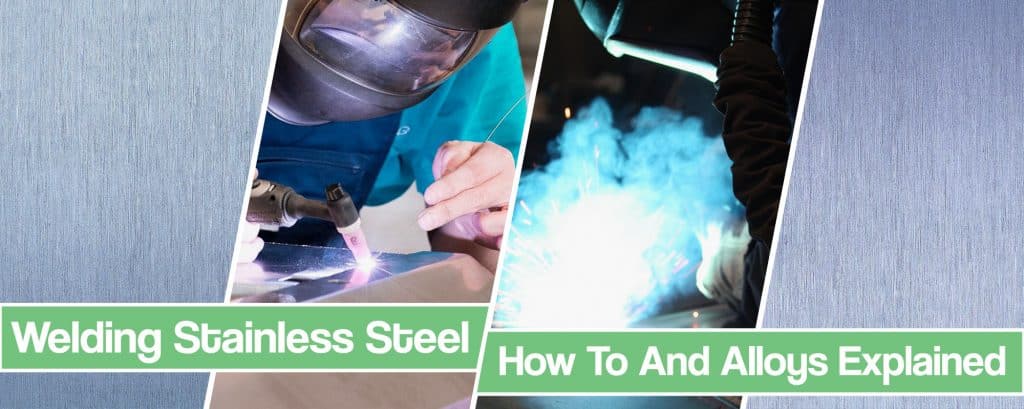
Today we will tell you all about the basics of welding stainless steel so you will know what to do when a project involving comes up.
Understanding Stainless Steel
Stainless still is an iron-based alloy that contains chromium. This substance is what gives stainless steel its most important property – corrosion resistance. The amount of chromium usually floats somewhere between 11% and 30%.
Each individual metal actually has different chemical attributes and combined with the amount of chromium present comes with different needs.
The usage of stainless steel is expanding thanks to its somewhat unique properties. It is a strong type of material that is resistant to various gases, liquids, and chemical corrosion and is for that reason used in many fabrication shops.
It is very durable and it does take a lot to actually tarnish it which is the reason why it has so many different applications. Unfortunately, mainly due to its favorable properties, stainless steel is also expensive. It costs five times more than mild steel.
Types of Stainless Steel
You may be surprised to learn that there is more than one type of stainless steel. Actually, there are five types that are characterized as stainless steel but most welders usually encounter three of them in their welding career. Each of them comes with its own characteristics and ways to weld stainless steel.
Austenitic Stainless Steel
Austenitic stainless steel is the most common type used today. It has non-magnetic properties and high weldability.
Its main usage comes within the standard fabrication and is used for more than 70% of production that we have today. It is labeled under the 300 series with the 304 being the most commonly used grade by far.
Range of composition: (C ≤ 0.10% – 16%) ≤ (Cr ≤ 28% – 3.5%) ≤ (Ni ≤ 32% – (Mo ≤ 7%)).
Austenitic Filler Metal Selection
AISI Steel | Recommended Filler Material | Alternate Filler Material |
---|---|---|
201, 202, 205 | 240 | 308, 347, 309 |
301, 302, 302B | 308 | 347, 309 |
304, 304L | 308L | 347, 309 |
304H | 308H | 347, 309 |
303, 303SE | 312 | 309MO |
316, 309S | 309 | 309CB, 310 |
310, 310S, 314 | 310 | 310CB, 310MO |
316, 316L | 316, 316L | 309MO, 317 |
316H | 316H | 309MO, 317 |
317 | 317 | 317L, 309MO, 318 |
321 | 347 | 309CB, 310CB, 321 |
347, 348, 347H | 347 | 309CB, 310CB |
320 | 320LR | 320 |
330 | 330 | - |
904L | 385 | - |
Martensitic Stainless Steel
Martensitic stainless steel is known for being the first type of stainless steel developed for commercial use. It has magnetic properties and can be hardened through tempering and quenching. The most popular usage of martensitic stainless still is in the production of cutlery.
It possesses chromium levels between 12% and 18% and a relatively high carbon content of 0.1% to 1.2%. Due to this, the 410 grade is used as a standard filler material choice for overlays on carbon steel.
Most of the martensitic stainless steel out there is welded with TIG Welding machines
Range of composition: (C ≤ 1.2% – 11.5%) ≤ (Cr ≤17%) – (Mo ≤1.8% – ≤ Ni ≤ 6% – V ≤ 0.2%)).
Martensitic Filler Metal Selection
AISI Steel | Recommended Filler Material | Alternate Filler Material |
---|---|---|
403 | 410 | 308, 347, 309 |
410, 410S | 410 | 308, 347, 309 |
414 | 410 | 410NM, 309 |
420 | 420 | 309 |
431 | 410 | 309, 310 |
440A | 312 | 309 |
Ferritic Stainless Steel
Ferritic stainless steel is known for being the cheapest type of the main three ones. Because of this, it is often used for making consumer products, auto parts, and sheet metal. It possesses magnetic properties and is very formable and highly ductile. Unfortunately, its greatest weakness is high temperature.
The automotive industry is the biggest consumer of ferritic stainless steel with grades 409 and 439 being used the most.
Range of composition: (C ≤ 0.08% – 10.5%) ≤ (Cr ≤ 30% – (Mo ≤ 4.5%)).
Ferritic Filler Metal Selection
AISI Steel | Recommended Filler Material | Alternate Filler Material |
---|---|---|
405 | 410 | 308L, 309, 410NM |
409 | 409CB | 430, 309LSi |
430 | 430 | 308L, 309L |
442 | 308L | 309L |
446 | 308L | 309L |
Preparing to Weld
When welding stainless steel, preparation is the most important part.
A welder needs to clean the material and their work areas thoroughly so there are no amounts of carbon steel present on the stainless steel material being worked on.
The same thing goes for your tools and welding machine, you have to clean them so no residue of carbon steel is found on them.
If particles of carbon steel end up in stainless steel, it can cause your final product to rust, ultimately defeating the purpose of using this material in the first place. Even trace amounts of carbon steel dust particles pose a threat. To learn more about welding prep refer to our separate guide.
Another thing to take into account when welding stainless steel is filler metals. The choice of filler material will depend on the type of base metal that you are working on. The best way to go about this is to use a filler metal with the same number as the base metal grade.
Common Stainless Steel Welding Methods
Choosing the right type of welding process for welding stainless steel depends on the finish, the thickness of the material, the base materials, and the use of the end product. Even though there are a variety of methods used the most common welding processes are TIG welding, MIG welding, and resistance welding.
TIG Welding or Gas Tungsten Arc Welding
TIG welding (Gas Tungsten Arc Welding) is the most commonly used type of welding process for welding stainless steel as it offers high-quality, longevity, and versatility. TIG uses low heat input, perfect for this type of material.
Preventing oxidation and increasing corrosion resistance can be done with a single-sided welding process. That way, inert backing gas protection is created between the interior and the exterior welds.
A full article about TIG welding can be found here
Resistance or Spot Welding
Resistance welding is great for stainless steel welding as it is the most economical welding process. The equipment used for resistance welding is versatile and can be used in various types of projects.
When spot welding, electrical current is used to heat up metal edges and join them together. This process is best used for materials with a low melting point as it can help in preventing distortion.
MIG Welding or Gas Metal Arc Welding
MIG welding is a semi-automatic process that results in a strong joint when it comes to stainless steel. MIG welding requires an argon shielding gas and a good welding wire electrode or steel wire. This process uses a pulsed current supply which allows the welder to get to some of the tougher spots of the base material.
Choice of Shielding Gas for Stainless Steel Welding
Choosing the correct shielding gas comes with several factors.
- Shielding efficiency.
- Resistance to corrosion.
- Metallurgy and mechanical properties
- Surface appearance.
- Weld geometry.
- Metal transfer.
Shielding Gas Choice
Shielding Gas, Plasma Gas | Backing Gas | |
---|---|---|
GTAW | Ar Ar + H2 (tot 20%) Ar + He (tot 70%) Ar + He + H2 Ar + N2 | Ar N2 N2+ 10% H2 |
PAW | Same as GTAW | Same as GTAW |
GMAW | 98% Ar + 2% O2 97% Ar + 3% CO2 95% Ar + 3% CO2 + 2% H2 83% Ar + 15% He + 2% CO2 69% Ar + 30% He + 1% O2 90% He + 7.5% Ar + 2.5% CO2 | Same as GTAW |
FCAW | No 97% Ar + 3% CO2 80% Ar + 20% CO2 | No Same as GTAW |
LBW | He Ar | Same as GTAW |
Ar – Argon, H2 – Hydrogen, He – Helium, N2 – Nitrogen, CO2 – Carbon Dioxide, O2 – Oxygen |
Checking the Temperature of Weld Metal and Base Metal
While welding stainless steel, you have to mind the temperature of both the base metals and the filler metal.
If you don’t monitor the surface temperature, you are more than likely going to end up with problems.
Monitoring the heat input to the base and filler metal can be done with the help of temperature-indicating sticks, electronic infrared thermometers, and electronic surface temperature probes.
Is Welding Stainless Steel Difficult?
Welding stainless steel is not so easy, especially for a beginner. This material is highly unforgiving when it comes to mistakes and high heat.
First of all, every scratch or blemish will remain visible. Mistakes are aesthetically visible and you might end up with an unattractive end product if you are not careful enough.
Secondly, stainless steel retains heat, making it susceptible to distortion and warping due to applied high heat while working on it. It can even warp because of the interpass temperature and during the cooling process if the heat is too great.
Working on stainless steel is thus left to more experienced welders that know how to handle it.
Frequently Asked Questions
Why Does Magnet Stick To 304 Stainless Steel and 308L Welding Wire?
This is normal. While some stainless steel types are non-magnetic, some contain a small amount of ferrite in the austenitic matrix to prevent hot cracking, and ferrite is ferromagnetic.
However, the 308L stainless steel welding wire is cold-worked during drawing which causes some transformation of the austenite into martensite, and martensite is ferromagnetic. But, melting the wire eliminates the martensite, leaving the weld-free from it, unless you cold work the welded joint.
Conclusion
Stainless steel is a material used all over the world for various reasons. It is one of the most important materials used today and its usage is not going to diminish any time soon. But you do need to be careful when working on it. If you treat it right, you will get the desired results.
- Stainless steel and its types https://www.stainless-steel-world.net/basicfacts/stainless-steel-and-its-families.html
- Common stainless steel welding methods https://www.atwf-inc.com/blog/3-common-methods-for-welding-stainless-steel
- Welding stainless steel https://www.worldstainless.org/Files/issf/non-image-files/PDF/Euro_Inox/BrochureWeldability_EN.pdf
- Filler metals for different types of stainless steel https://www.wmwa.net/metal-products/filler-metal-charts/
- The wide world of welding stainless steel https://www.thefabricator.com/thewelder/article/metalsmaterials/the-wide-world-of-welding-stainless-steel