Are you feeling overwhelmed by trying to work out what is plasma cutting? We know that it can seem like a really complicated area of work when you first look at it.
Even the terminology can seem odd, like what’s a “swirl ring” when it’s at home?
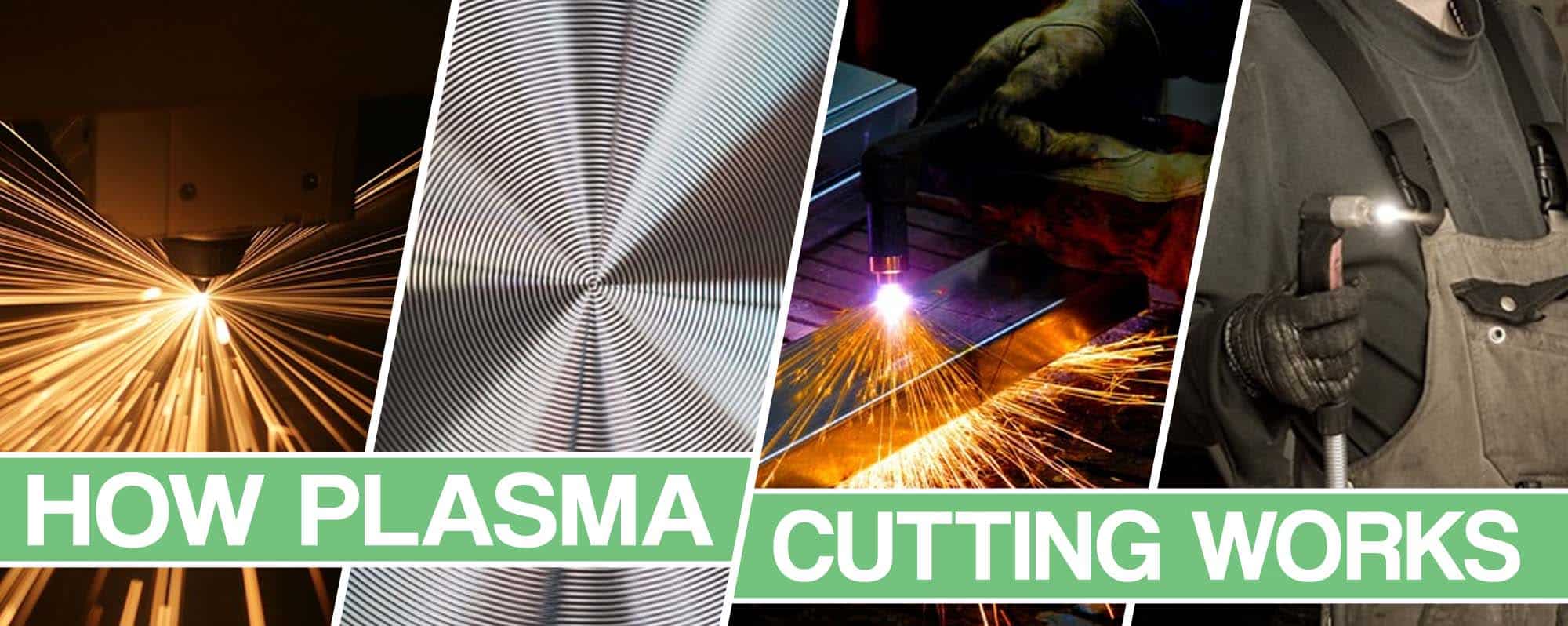
Fortunately, once you get under the surface a little – it’s not quite as complicated as it initially appears. While the technology used is very impressive and the output temperatures are incredible, the practical application of plasma cutting is quite straightforward.
So, we’ve put together a super guide for you for everything you need to know about plasma cutting. It walks you through the basics from “what is plasma?” and then leads you through all the nuts and bolts of how plasma cutting works before wrapping up with some of the questions that people frequently have about this work.
We promise that it will all become clear by the end and you’ll be able to explain plasma cutting just like an old hand.
What Is Plasma?
Before we can talk about how plasma cutting works, we first need to address the question, “what is plasma?”
You may have heard of three states of matter when you were at school: Solid, liquid, and gas. Well, there are more than three and plasma is the fourth state of matter.
Matter moves from one state to another when you add energy to the molecules or atoms of the material. So, if you heat up ice, for example, it melts and becomes water.
Then if you heat it a little more it becomes a gas, or steam as we usually refer to water vapor. Finally, if you heat it, even more, the gas becomes separated into ions and at this point, it will conduct electricity and is considered to have become a plasma.
What Is A Plasma Cutter And How Does It Work?
In simple terms, plasma cutters push an electric pilot arc through a narrow opening which is filled with gas. Plasma gas can be any choice of oxygen, argon, shop air, nitrogen, etc.
This process heats up the gas to a temperature sufficient for it to transition into a plasma, the fourth state of matter.
As an electrical conductor, the plasma can then form a circuit with the metal (or other material) that is being cut and this causes the plasma arc to be able to cut through the material.
The restricted opening is known as a nozzle. This narrow opening forces the gas through at a very high speed, and the very high-temperature gas passing through the nozzle onto metal allows it to slice through the metal in much the same way as a knife passes through butter.
The pilot arc, which is produced in most high-quality plasma cutters, acts between the electrode and the nozzle to ionize the gas before the arc transfer begins.
In lesser models of the plasma cutter, you may find that the plasma creation begins when the torch tip is used to force a spark by being touched to the metal surface or it might use a starting circuit (a high-frequency design which is very much like a spark plug in a car engine). It’s worth noting that you can only use a plasma cutter that takes advantage of a pilot arc to run CNC cutting machines.
Handheld Operation
If you want to use a handheld plasma system(110v/220v plasma cutting machines), it’s a good idea to know that when the system is in the OFF state, the nozzle and the electrode are going to be touching within the torch.
As soon as you squeeze the trigger, you produce a DC current from the power supply which will then flow through the connection, and at the same time, the plasma gas begins to flow.
The plasma gas then builds up pressure within the nozzle until it is sufficient to force the nozzle apart from the electrode. This creates the pilot arc that allows the gas to become a plasma jet.
As soon as this takes place, the DC current flow switches from the electrode and nozzle and forms a path between the electrode and the workpiece being cut. This will remain in place until such a time as the trigger is released at which point it returns to the OFF state.
Precision Plasma Operation
The video above demonstrates one of the systems of precision plasma cutting on the example of ESAB.
In a precision plasma torch, things are different. The electrode and nozzle are kept apart by the use of a swirl ring. This is a ring with tiny venting holes that push the preflow of plasma gas into a vortex.
When the power supply is started, it creates up to 400 Volts DC of open-circuit voltage. This then sets the plasma gas flowing into the torch. At this moment, the nozzle temporarily connects to the positive potential of the power supply and forms a pilot arc circuit. The electrode, of course, is forced to the negative potential at this point. Then a spark of high frequency (again rather like in a spark plug) is created by the Arc Starting Console.
This spark allows the plasma gas to become ionized and it gains the ability to conduct electricity forming a full pilot arc. As soon as this arc is in contact with the workpiece, then the current shifts to connect the electrode with the metal being cut. The workpiece is always rested on a cutting table that has been fully grounded to prevent the current from flowing elsewhere while you work.
This changes the DC current to produce the correct amperage, as selected by the user of the plasma cutter, and switches out the preflow of gas to the optimal blend of gas for the material that you are cutting. Then a secondary gas, a shielding gas, is fed through the nozzle to further focus the plasma arc – this allows for a super clean cut which keeps the bevel angles as low as possible and reduces the kerf.
Plasma System Components
There are 5 key components of the plasma system:
The power supply
The power supply – this will convert either single or three-phase AC line voltage into a useful DC voltage of up to 400 VDC. This ensures that the plasma arc stays stable throughout the arc cutting process.
Arc Starting Console
The Arc Starting Console – this is a simple circuit that is designed to deliver an AC voltage of around 5,000 VAC at 2MHZ (which is very high-frequency) to produce the spark that launches the plasma arc
Gas
Gases – gas flow is essential and plasma systems can use nearly any gas but typically nitrogen, shop air, oxygen, argon, etc. these can serve two purposes: 1. to form the base of the plasma arc or 2. to shield the plasma to provide a better cutting experience
Cooling
Cooling system – plasma cutters become so hot that if they didn’t have a cooling system the nozzle or electrode might catch fire, thus a liquid cooling system is used to keep the temperature under control at all times
Torch
Plasma torch – the plasma torch is designed to enable the proper alignment of the plasma arc and to ensure that the cooling system operates effectively. Consumables for a plasma cutter include nozzles, the electrode, and the swirl rings.
Material Considerations
You can only cut objects that are electrically conductive with a plasma cutter. This is because the material forms part of the circuit for the plasma arc. If it’s not electrically conductive – there is no circuit and no cutting.
That means it’s suitable for most metals including:
- Structural steel, stainless steel, non-alloy, high-alloy, and low-alloy steel
- Clad metal plates
- Aluminum
You may also use a plasma cut on brass, cast iron, copper, and titanium but the melting temperatures of these materials can interfere with delivering a quality cutting edge.
You can use plasma cutters to cut through material from 0.5 mm to 180 mm thick though this varies between plasma cutting machines and materials.
The Plasma Arc Cutting Process
There are many variants of the plasma arc cutting process but the basic principles of this process remain constant whether you are cutting stainless steel, structural steel, alloy steel, copper, or any other material or sheet metal.
This process has five distinct phases:
Initiation
Pilot Arc Initiation – this is the moment when the start command is given and at which the initial arc is generated to trigger the inflow of gas to the electrode and to force it out through gas nozzle.
Main Arc Generation
Main Arc Generation – the next step is to ignite the arc and ensure that the electric arc is formed between the electrode within the plasma cutting machine and the workpiece itself and at this point, cutting begins and at the same time if two plasma gases are required, the shield gas will start to flow to hone the cutting flame.
Local heating
Localized Heating and Melting – then as the plasma gets to work, the temperature rises and it causes the localized heating and melting of the workpiece but it may also trigger problems within the nozzle and thus a cooling system is required at this point.
Material ejection
Material Ejection – the weakened material from the workpiece is then expelled from the kerf using kinetic energy which is supplied by the plasma jet gas flow.
Movement
Arc Movement – then after the material is ejected the plasma arc is moved across the surface of the material until the cutting process is complete.
Variants Of The Plasma Arc Cutting Process
As a general rule of thumb – the process for plasma cutting is the same no matter the variant. That said, each cutting variation gives a specific advantage depending on the application it is used for
The variations are considered to be different ways of utilizing cutting plasma based on the cooling system, the electrode design in the plasma torch, the plasma jet gas used, or the final type of cutting plasma deployed.
Some of the options available are:
Standard
Standard/Conventional Plasma Arc Cutting – the nozzle opening is the only thing used to constrict the plasma arc and there is no secondary medium deployed (the coolant is typically water or air).
With secondary medium
Plasma Arc Cutting with a secondary medium – this is when a secondary medium (that is another medium) is drawn into the plasma torch to further constrict the plasma arc and to provide particular characteristics that depend on the application for which the plasma jet is being used.
With water injection
Water Injection Plasma Arc Cutting – in this form of plasma arc cutting water is injected into the plasma arc giving it a substantial temperature boost via the gas nozzle to about 30,000 degrees centigrade and this can improve the quality of the cut provided.
Advantages And Disadvantages Of Plasma Cutting
The advantages of plasma cutting include:
- It depends on the series of the plasma cutting machine but you can often operate one or more burners simultaneously
- You can cut through any material which offers conductivity to electricity
- You can easily cat high-alloy steel, aluminum, and similar materials in either medium or large thicknesses
- You get superb performance with small and medium mild steel at any thickness
- You can plow through high-strength structural steel without as much heat as in other cutting methods
- Plasma cutting speeds are about 10 times faster than oxy-fuel cutting
- It allows you to effectively process a high-quality blank for thick and medium sheet metals
- Plasma arc cutting is ideal for the automation of the cutting process
- When plasma arc cutting underwater – it creates a very low level of noise and produces a very low heat exposure too
The disadvantages of plasma cutting include:
- You’re still restricted to a maximum cut of 180 mm when dry plasma arc cutting and only 120 mm when working underwater
- You still get a somewhat wider kerf than ideal
- The power consumption for plasma arc cutting is high
- It doesn’t offer the same quality cuts as laser cutting does
- It is rather more expensive to run than an oxyacetylene system
- You may find that dry cutting is noisier than you’d prefer
Frequently Asked Questions (FAQs)
Are Plasma Cutting Fumes Dangerous?
While, technically, the fumes from plasma cutting are not dangerous – the fumes from the cut metal are dangerous. Most metals when burned in the air will form toxic deposits that should not be inhaled, even Iron Oxide (rust) when inhaled can accumulate in your lungs and do real damage to your health over time.
Do You Need A Welding Mask For Plasma Cutting?
Officially? No. You could get away with just wearing safety goggles for plasma arc cutting but we’d recommend that for must plasma cutting that you wear both safety goggles and a welding mask. This gives your eyes maximum protection whatever cutting method you are working with.
Can A Plasma Cutter Cut Wood?
What is plasma cutting? It’s the use of plasma arc cutting to cut materials and for that to happen effectively, it requires the material that is being cut to be electrically conductive. If it’s not electrically conductive, the arc will fail – wood isn’t electrically conductive and this, a plasma cutter cannot cut wood.
Will A Plasma Cutter Cut Rusty Metal?
Yes, because rust conducts electricity just as well as any other type of metal so the plasma arc cutting process is not impeded at all by rust. It will put the same quality cuts in dirty steel, rusted steel, and even painted steel just as well as it would cut something like stainless steel.
Are Plasma Cutters Dangerous?
Yes. The heat generated in plasma arc cutting is incredibly intense. There are risks to your eyes (you should always wear glasses with a side shield and a welding helmet), your clothing (you need to use fire-resistant suits), and even your feet and hands (special gloves and shoes are required).
Even with all this, there are risks of sparks or molten metal creating fires in the workplace or on the cutting table.
How Thick Can A Plasma Cutter Cut?
It depends, to some extent, on the machine and the material involved. However, your average hand-held plasma torch will happily produce a plasma arc cutting through up to 38 mm of thick steel or stainless steel plate.
If you use a computer-controlled plasma torch, however, they can go do plasma arc cutting of up to 180 mm thickness.
What Does The Future Hold For Plasma Cutting?
In the present day, you can use high-end plasma cutters to work their way through an incredible 200 inches of metal plate in a single minute. They produce 40,000 degrees of heat while they do it.
That’s nothing. Scientists have now shown that you can produce a cutting plasma of up to 10 trillion degrees. Of course, it’s highly unlikely that such a cutting plasma tool would ever be needed to slice through metal but it does show that there is a tremendous amount of potential for this technology in the future.
The current problem with the plasma cutter is the mess that it leaves behind – dross to be precise. This is a sort of residue that is produced by the molten metal which sticks to the corners of the metal and diminishes the cut quality substantially.
The cut quality of laser cutting equipment or water cutting equipment, in contrast, is much higher than that produced by plasma cutting. That means no finishing work is needed when the cutting is done.
If you were to ask some workshops, “what is plasma cutting?” they’d reply that it’s a generator of finishing work. They’d rather use the laser cutting equipment or water cutting equipment in their work but these machines are expensive, are generally not available in portable ranges, and take up to 100 times longer to do the job than a plasma cutter.
So, the hoped-for future of plasma cutting is for a cleaner finish to the cuts that they produce. If they can manage this, whilst maintaining the speed of plasma cutting as it is now, they will be an unrivaled force in the cutting world.