Welding cast iron is and was always a challenging feat, particularly if you are an inexperienced welder. However, being able to do it by yourself could save you a lot of time and money.
If you are planning to do some in-house cast iron welding, you should research the topic and get acquainted with all the ins and outs of the process.
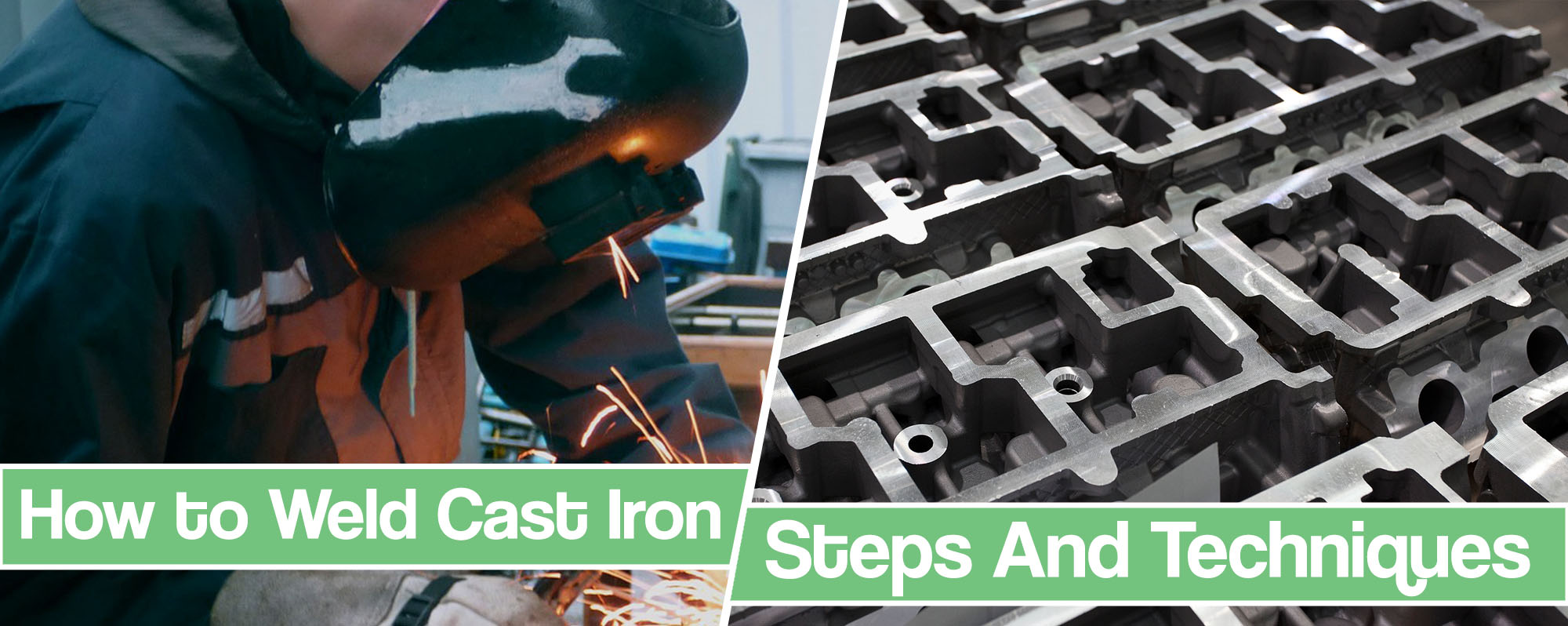
It is not as easy as you would think (but not as hard as it was in the past). Lucky for you, this article contains everything that you need to know about successfully welding cast iron.
The Key Steps in Welding Cast Iron
If you notice a crack on a cast iron piece that you possess, you can easily fix the problem. However, a lot of people seek the help of skilled welders and welding facilities for these types of fixes. Knowing how to weld cast iron is a valuable skill to have and not a lot of people are able to do it properly.
That said, it is not impossible to learn how to do it. It takes time and practice and at a certain point, you might build up enough skill and learn how to do it properly.
Most Important part – Identify the Alloy
Cast iron is every alloy that consists of iron, carbon, and silicon. The amount of carbon present needs to be higher than 1.7% and lower than 4.5%. The high carbon content is what gives cast iron parts their characteristic hardness.
Unfourantely, cast iron also comes with some cons which include low ductility and it being less malleable compared to steel, stainless steel, or wrought iron.
Some types of cast iron are also easier to weld than others.
Usually, during a welding process, the cooling and heating process will cause the material to contract and expand, inducing tensile strength in the metal. However, cast iron is not able to stretch nor deform. Instead, it cracks which makes it very hard to weld properly. Luckily, these characteristics can be improved by simply adding different types of alloys.
Grey Cast Iron – Most Common And Weldable
Grey cast iron is the most common form of cast iron. It has low ductility, meaning that it will not expand and is susceptible to cracking. During manufacturing, carbon precipitates out into graphite flakes into a pearlite or ferrite crystalline microstructure.
Actually, it is much more weldable than white cast iron but it can still be difficult to weld even for the most experienced welders. This is because of the graphite flakes that can enter the weld pool to cause weld metal to become brittle.
White Cast Iron – Non-weldable
As far as white cast iron goes, it retains the carbon as iron carbide and doesn’t precipitate it as graphite flakes. Its cementite crystalline microstructure makes this material very hard and brittle at the same time. Many welders consider white cast iron as virtually unweldable.
Ductile, Nodular, or Malleable Iron – Hard To Identify – Weldable
These types of cast iron are considered to be less brittle because of microstructural differences during their manufacturing process. Due to the unique manufacturing processes used, they have spheroidal carbon microstructures.
Determining the alloy type
The most reliable way is to simply check the metal specification or using the Spectrochemical analysis. This is not usually available so you could also revert to some basic methods.
Along with the fracture point, the grey iron will usually show a grey color because of its graphite microstructure. This only works if you know that your metal is grey or white iron.
When working with ductile iron this will not be as simple as it is white along the fracture while being much more weldable.
How to perform spark testing
The spark testing is usually performed by an experienced metallurgist and it determines the type of cast irons that you are working with. Below is a nice visual summary of how it works in practice.
Cleaning the Casting
Cleaning the casting and preparing it for welding is a crucial piece of the puzzle. This goes for all alloys, not just cast iron. You should remove all surface materials first and make sure that the weld area of the casting is completely clean. Paint, grease, oil, and other foreign materials should be thoroughly removed.
It is best that you apply heat as carefully and as slowly as possible to the weld area for just a bit so you remove any entrapped gasses from the weld zone.
A good technique that you can use to see if the cast-iron surface is ready for welding is to deposit a weld pass on the metal. It will be porous if there are any impurities on it. You can then grind the pass and do it a few times until the porosity disappears.
Pre-Heating the Cast Iron
All types of cast iron are susceptible to cracking under welding stresses. If you want to avoid cracks, you need to manage heat control.
Thermal expansion is the biggest problem here because when you warm the metal up it will expand. There is no stress if the object warms and expands at the same rate. However, stress starts to build when the heat is localized in a small heat-affected zone. Therefore, localized heating can restrict the expansion of the heat-affected zone.
Steel and other ductile metals stress created by restricted expansion and contraction can be relieved with stretching. Unfortunately, contractions can also cause cracking due to the poor ductility of cast iron. Pre-heating will decrease the thermal gradient between the casting body and the heat-affected zone. This will result in minimizing the tensile stress that welding creates.
Preheating will soften the area next to the weld. It will degas the casting and reduce the porosity of the deposited weld metal. Additionally, it will increase welding speed.
Finishing it Up and Cooling Process
While the weld of the cast iron that you are working on cools down and contracts, the tensile stress can build up. Thus the thermal contraction phase is the part where cast iron is the likeliest to crack.
The best way to reduce cracking is to apply compressive stress that can oppose tensile stress during the cooling process. In that case, welders use a technique called peening which involves moderate strikes with a ball-pen hammer. They use the hammer on a deformable weld bead while the weld is still soft. Penning will decrease the risk of cracking but can only be applied when working on a relatively ductile weld metal.
After you are finished working on a cast iron weld, cool slowly. A slow cooling rate can be achieved by wrapping the casting in an insulated blanket or by burying it in the sand. DIY welders may also use a Charcoal BBQ and place it in a bucket of sand. A good method is placing the welded pice onto a wood fire oven which will allow it to cool down as the fire dies out.
Choosing the Welding Process and Filler Material
When it comes to cast irons, one should choose a proper welding technique. Some of the most common welding techniques are stick welding, oxy-acetylene, and braze welding.
Arc Welding Cast Iron
The most preferred method for welding cast iron is the shielded arc metal welding process. There are four types of filler metal that are going to be used: cast iron-covered electrodes, covered copper base alloy electrodes, covered copper base alloy electrodes, and mild steel covered electrodes.
You will need to pick one of these depending on the machinability of the deposit, the strength of the deposit, the color match of the deposit, and the ductility of the final weld.
Cast Iron Electrodes
Welding with cast iron electrodes requires you to preheat between 250 and 800°F (121 and 425°C). The heat input will depend on the size and the complexity of the casting and also based on the need to machine the deposit and the area around it. The more heat you apply the easier will it be to machine the weld deposit.
It is advised that you use small size electrodes and a low current setting. Also, use a medium arc length and try welding metal in a flat position. You should also apply wandering and skip welding procedures while penning will reduce stress and minimize distortion.
Nickel Based Electrodes
Nickel electrodes can be used without preheating, but it is still advisable to heat them to 100°F (38°C). You can use these electrodes in all positions but they still work best in the flat position. Remove the welding slag between welding metal passes.
Nickel Rod 99%
The 99% nickel welding rod is the specialty nickel wire and is considered the cream of the crop for iron cast welding. They are expensive but are also the best when creating machinable low to medium phosphate content.
Nickel Rod 55%
The 55% of welding rods are practically a cheaper version of the 99% ones. They come with a lower coefficient expansion which produces less stress and fewer fusion cracks. They are very good when working on thicker pieces of metal and they are also machineable.
Mild Steel Electrodes
If you are planning to machine the deposit then you should avoid using mild steel electrodes. The mild steel will pick up enough carbon to make a high-carbon deposit, making it un-machineable. The deposit will also have reduced ductility. These types of electrodes should only be used for small repairs with minimum pre heat required.
TIG Welding Cast Iron
TIG welding is possible thanks to the nickel wire availability. This filler metal is expensive but the benefit is that by using it you can achieve very strong and clean welds. The pre and post-heating may be avoided if you select a proper wire and gas.
In order to prevent welds brittleness, you should use a gas mix of 75% argon and 25% CO2.
MIG Welding Cast Iron
MIG process can be applied when welding together malleable iron and carbon steels. It should never be used with big diameter wire and should be used with low amp settings. You can use the following wire for electrode:
- Mild steel – Use with 75% argon and 25CO2.
- Silicon bronze – 50% argon and 50% helium.
- Nickel copper wire – 100% argon gas.
Gas Welding Cast Iron – OxyFuel
This method uses electrodes too but the source of energy is an oxy-acetylene torch. The best electrodes for this method are the cast iron and copper zinc electrodes.
You should be careful not to oxidize the piece when working with the acetylene as this will cause silicon loss and the white iron will form. In order to bring temperature gradients to a minimum, you should melt the rod in the molten welding pool instead of applying it directly to the flame.
Braze Welding
This is a widely used method for joining together cast iron elements thanks to its low impact on the metal. A brazing rod is a filler that adheres to the cast iron surface. Due to the lower melting point of the brazing wire, the filler will not dilute with the cast iron but will adhere to its surface area.
You must clean the surface as best as you can as this is a crucial element here. If the surface area of the joint is not clean the braze weld will not have proper adhesion.
Additional Tips and Techniques
Now let’s see some pro ideas that will improve your success and overall strength of the connection joint.
There are many things that you could do to further improve the quality of your work but here are the two most commonly used.
Using a V groove
If you will be using a groove, a V groove of 60-90° angle is to be used. You should extend the groove to about 1/8 of an inch from the bottom of the crack. Additionally, small holes need to be drilled at the ends of the crack in order to stop the crack from spreading further.
Studding the joint
If you are repairing a large casting then applying studs might be beneficial. First, you will need to make a V groove using a grinder although.
At each side of the groove, you need to drill and tap a-holes and then screw the stud into each of these holes for a distance equal to about the diameter of the studs. The upper ends of the studs need to projet about 1/4 of an inch above the surface.
Then these studs need to be seal welded by a bead or two around each of them and then further tied together with weld beads.
Welds should be applied in short distances and each needs to be peened while it is hot. This is done to prevent stress or cracking upon cooling.
Conclusion
If you are thinking of doing any kind of a job that involves welding cast iron, be sure to prepare yourself first. Whether you are working on construction machinery or a simple sidebar, you have to apply the proper technique to do the job well. The most important part to remember is that rapid cooling is bad and weld cools need to go slow.
Cast iron is one of the most difficult metals to weld but it is not impossible to do it. As long as a welder applies proper technique, they will be fine.