TIG Welding (Tungsten Inert Gas), besides MIG welding, is one of the most used welding methods that people employ! But when is it appropriate to use this method?
In fact, TIG welding has an advantage over other methods as it can weld a wider variety of metals.
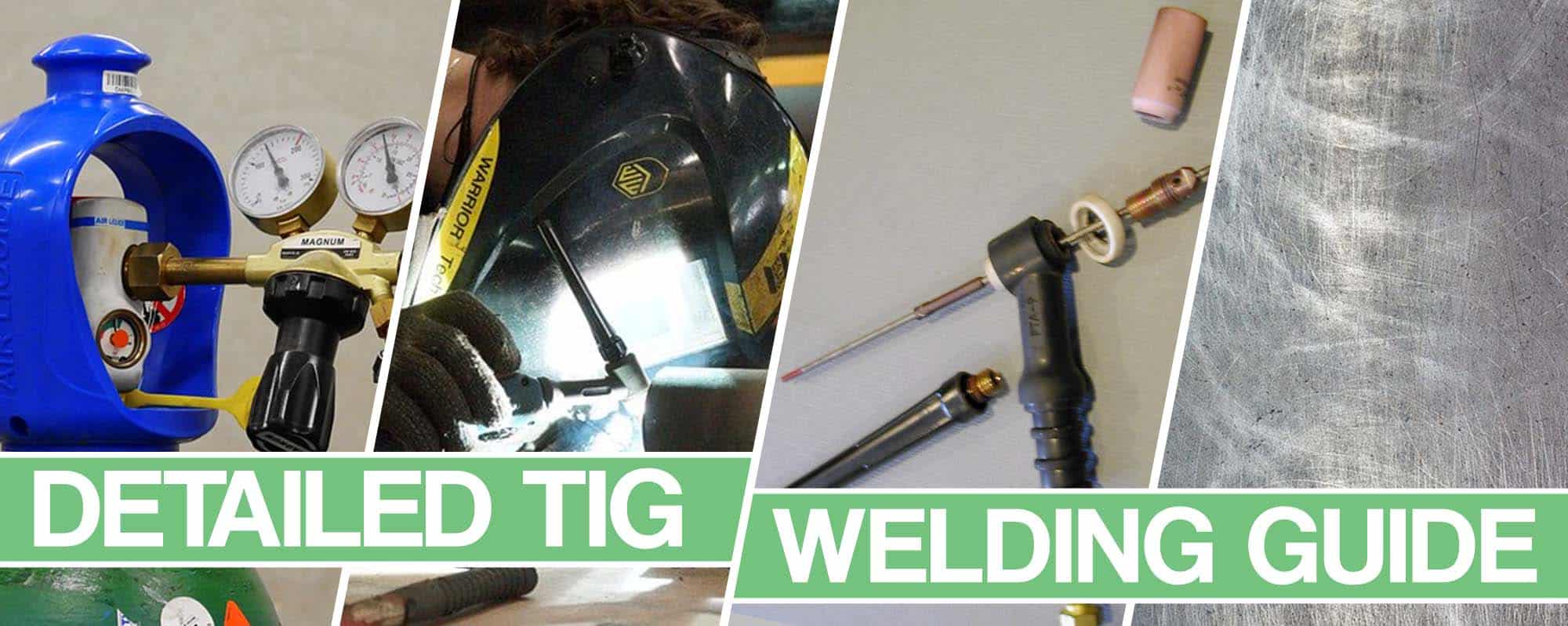
It is a clean method that provides a good-looking finish without creating the messy splatter that most methods come to make. If appearance is what the welder is aiming for then this is the method to choose.
But how to successfully employ this method of welding?
I will tackle this problem and explain everything there is to know about TIG welding in the following lines…
What is GTAW or TIG Welding About
TIG Welding, also known as Gas Tungsten Arc Welding (GTAW), is a process that includes the use of an electric arc combined with a TIG electrode. The electrode itself is made out of tungsten, meaning that it does not dissolve when welding. Old-timers used to refer to this method as Heliarc welding because they used helium as a shielding gas.
The process itself includes a non-consumable tungsten electrode that carries current to the welding arc.
Both the weld pool and the tungsten are shielded using an inert gas (usually pure argon gas). This type of process is comparable to oxy-acetylene welding because both of them use filler material for reinforcement.
TIG welding is a process that requires the welder to use both arms. One hand holds the TIG torch while the other adds the filler rod to the weld joint. This makes TIG welding the most difficult process to learn. But after learning it, it becomes the most useful process that one can acquire due to its versatility.
Types of materials that you can weld include steel, stainless steel, aluminum, nickel alloys, chrome alloys, copper, brass. magnesium, bronze, and even gold.
The process is slow, but when done right it provides the most beautiful weld, aesthetically speaking, and a high-quality one as well.
How TIG Welding Works?
Generally speaking, TIG welding is the process of fusing metal with metal. It requires three things – heat, a shielding gas, and filler metal.
The heat is created by the electricity passing through the tungsten rod. The shielding is added through a compressed bottle that provides gas flow to the weld area. The filler metal is a simple wire that the welder feeds and dips by hand which is then melted into the arc.
In one hand, a TIG welder holds a TIG torch that is aimed at the area where one needs to start welding. The other hand is reserved for the metal filler rod. Finally, our foot hovers over a pedal that you use to start everything.
By pressing the pedal an electric current will shoot out of the torch gun and create an immensely high temperature.
At the same time, the filler wire is fed into the weld pool and melted. At the same time, the machines provide an inert gas with the aim of creating a barrier bubble that will, in turn, keep all the impurities coming into contact with the molten metals. Keeping everything clean.
There are several parts of welding equipment that a TIG welder needs to be familiar with though. The work lead, or the ground cable with a clamp, is attached to the workpiece. The welding lead comes with a TIG torch at the end. There is a small line along with the cable that supplies the argon gas. Finally, a gas bottle and a regulator are also necessary.
The TIG Welding Torch
The TIG welding torch(1) is comprised of several parts! The electrode is the small tungsten rod that usually comes available in several sizes. The main difference is that the electrode does not burn up like a filler rod. Instead, you can sharpen the tungsten to a point or a ball shape. It all depends on what you are working on.
There is a copper collet that holds the tungsten that is used to adjust the length it protrudes from the cup. The cup is ceramic and is replaceable if necessary. There are also several cup outlet diameters offered.
The collet-body has several cross-holes which are used to feed the gas to the cup and surround the tungsten. It is supposed to exclude oxygen as it could contaminate the weld.
TIG Torch Types
There are two types of commonly used torches for TIG welding – Air-cooled and water-cooled TIG torches.
- Air-Cooled TIG Torches: These types of torches are very practical and are not as expensive. The problem with it is that that it can heat too much. It can be tough to hold and a lot of the heat goes wasted.
- Water-Cooled TIG Torches: These types of torches are much more efficient, but besides water coolant, they require a lot of maintenance. It requires a water cooler and inside it, there is a radiator that the water passes through.
The Tungsten
Tungsten is a hard but also very brittle type of metal. Compared to other metals, its uses are very limited but has found its use in TIG welding. Tungsten is used in making the non-consumable electrode for the arc for TIG welders.
Thanks to Tungsten’s unique properties the arc is able to maintain a temperature of 11,000 F (6,000 C). Tungsten has a high melting point and excellent conductivity. Although very strong, it is brittle and can be easily broken with a tap.
Tungsten Electrode Types
As the name states, Tungsten is the main ingredient of the electrode. But there are other elements that are added in order to create different effects. The most commonly added elements are Cerium, Lanthanum, and Zirconium.
- Pure Tungsten: Used with an A/C alternating current exclusively for magnesium and aluminum welding only. It comes with a green AWS tip and an EWP classification code.
- Zirconium Tungsten: Although it does have similar properties to pure Tungsten it is still very much different. The usual mixture ranges from ¼% Zirconium Oxide up to 1/2% Zirconium Oxide, while the rest is pure Tungsten. It is also usually used with an A/C alternating current to weld aluminum and magnesium. The tip is brown and comes with an AWS classification of EWLa-1.
- Thoriated Tungsten: Typically used with a direct current and an electrode negative polarity (DCEN). The addition of Thorium Oxide allows the electrode to carry more current and lower temperatures, allowing for easier arc starting. Thoriated Tungsten can weld most types of metals except magnesium and aluminum. 1% mixtures have a yellow AWS tip and an EWTh-1 classification. 2% mixtures come with a red AWS tip EWTh-2 classification.
Shaping Tungsten Electrodes
Tungsten rods come with a square cut end, so they have to be shaped. The geometry of Tungsten affects the arc shape, arc length, the point longevity of the electrode, and weld penetration. therefore, electrodes are usually pointed, rounded or tapered with a ball end.
Electrodes with a Pointed Tip
Pointed tips in TIG welding are usually used for welding steel. It usually uses the Direct Current Electrode Negative (DCEN). This type of tip allows the current to flow from the electrode to the metal and concentrate the arc temperature onto the metal.
Sharpening a pointed tip is done on a grinding wheel or e specific Tungsten electrode sharpener. But using the grinding wheel comes with its downsides. Since Tungsten is slightly radioactive, it is dangerous to breathe in the particles that are created. Tungsten should be ground straight on the wheel and not at a 90-degree angle. This ensures that the grind marks run straight the length of the electrode. This eliminates ridges that can cause arc wandering and contaminate the weld puddle by melting in it.
Electrodes with a Balled Tip
Generally, balled tip electrodes in TIG welding are used on pure tungsten and zirconiated electrodes. It is better to use them with the AC process on sine wave and conventional square wave GTAW machines.
In order to create a ball shape at the end of the electrode apply the DCEP amperage recommended for a given electrode diameter. This will cause a ball to be formed at the very end of the electrode. Applying too many amps will fry the Tungsten. The diameter of the balled tip should no go over 1.5 times the diameter of the electrode.
Having a larger tip than necessary will reduce arc stability and may also fall off. This could contaminate the weld puddle and you definitely don’t want that to happen.
TIG Filler Metal/Wire
When it comes to welding TIG the most commonly used filler rod for aluminum base metal is the 4043 alloy. But in order to color match welds and anodized parts, a 5356 one is much more suitable.
A filler material with a copper coating is the most suitable one for TIG welding. Similar to oxy-acetylene welding, using copper as a filler rod during the welding process will help to prevent the material from rusting.
TIG Welding Shielding Gasses
Like with any other type of welding process, a shielding gas for welding TIG is needed to protect the weld pool from impurities and potential contamination. The most commonly used types of gases for TIG welding are Argon (Ar) and Helium (He).
Pure Argon is the most commonly used one of the two and is best applied for gas welding aluminum and carbon steel. But the gas needs to be completely inert. So shielding gases used for TIG welding, or any other gases that have CO2 are not suitable. CO2 is an active gas and when mixed with Argon will oxidize and thus damage the Tungsten.
Flow Rate – TIG welding requires a lot of gas for shielding so the welder needs to set the gas flow accurately. A flow rate of 6 to 7L/min is usually enough. But it can be increased if necessary, usually when welding in drafty conditions.
Post-Flow Time – Postflow is important for protecting both the Tungsten and the weld as they cool down. The higher the amps the more time will it take the Tungsten to cool down. So to be sure that you have done this right, welders usually take 1 second for every 10 amps of post-flow time to make sure that the weld and the Tungsten are cooled.
How TIG Start Works?
There are three commonly used methods to start the arc. They include Scratch Start, Lift Start, and High-Frequency Start. The most used one is the High-Frequency start though. HF start can be made by a foot pedal or a button on the TIG torch.
Scratch Start
The scratch start method is probably the oldest method in existence for starting the arc. It’s almost the same as sparking a match. It involves flicking Tungsten across some metal until the arc starts.
It is definitely not a pretty process but also an unsuitable one for TIG welding. Scratch start causes some small bits of Tungsten to break off. The heat of the Tungsten rises almost instantaneously when sparked. While your welding helmet will protect you it may contaminate the weld pool, and we don’t want that to happen.
Lift Start
Lift start gets often confused with a scratch start. But the two methods are completely different from one another. Lift start is a much cleaner method for TIG welding, even though it also involves making contact with the metal.
The Tungsten needs to make slight contact with the metal, followed by a very fast lift to draw the arc. At this point, the OCV of the welder goes back to a very low voltage output when the unit senses that it has made contact with the workpiece. As you draw it back, the unit will immediately hit a higher voltage output as it leaves the surface.
However, the problem with this method is that it is still not 100% clean. Even though the touch is short, there is still some possibility of contaminating the weld. Still, it is much better than the scratch start method and is suitable for welding steel and stainless steel. But it should not be used for welding Aluminum due to the reaction that Tungsten and Aluminum have towards one another.
High-Frequency Start
The High Frequency start method is the cleanest and most preferable one for TIG welding. The start is achieved by a high-frequency arc is able to ionize the air. So there is no need for making contact between the tip of the Tungsten and the work piece.
Although this is a touchless method, contamination is still possible. It could happen if the Tungsten tip is too sharp or if the amperage is turned up too high when starting the arc.
High-frequency start is the only choice when welding Aluminum and is also a suitable option to weld AC or DC.
TIG Torch Foot Pedal Remote Start for HF Start
Foot pedal remote starts can be a bit complicated but generally, work as the gas pedal in your car. The foot-operated pedal controls both the high frequency start and the amperage. So the more you push, the more power you will get.
It is best used when sitting down, as welders will have a hard time using it by standing.
The video below demonstrates how it works.
The best part about the TIG torch foot pedal remote start is that it allows you to fully control the heat. TIG machines come with foot-operated amperage control. Welders can pre-set the maximum amperage and use the pedal to lower it or bring it higher, but never going across the maximum setting. This comes as more than useful when welding alloy steel.
The best thing about the remote foot pedal is that it allows the welders to initiate the heat slowly and also gently bringing back down. Doing it abruptly can cause thermal shock that many alloy steels is sensitive towards. This can result in a brittle weld and not quality work.
TIG Welding Voltage Types and Polarities
TIG welding uses the same types of voltage types as stick welding does – DC and AC. DC (direct current) is the type of current that car batteries run on and flows in one direction, from negative to positive. AC (alternating current) is the same one found in our homes and it changes directions many times.
As far as TIG welding goes, it uses two DC polarity types:
- DC Direct Current Electrode (-) Negative: The negative side of the circuit is in the welding handle and the electricity flows from the TIG torch to the work piece.
- DC Direct Current Electrode (+) Positive: The welding handle is positive and the electricity that flows from the welding metal to the TIG torch is positive.
The difference that the polarity makes is directly connected with how much heat is applied to the electrode.
- DC electrode (-) negative creates 2/3 of heat onto the metal. This results in a deeper penetration weld. It helps in preventing the overheating of the Tungsten.
- DC electrode (+) positive creates 2/3 of the heat onto the electrode. The result is a shallower weld, more suitable for sheet metal work. It also provides a cleaning action at the same time.
Important TIG Machine Settings
There are a few settings that a TIG welder has to keep in mind when setting up their equipment. It will still differ from machine to machine but there are still some general ones to keep in mind.
A/C Frequency
This setting allows you to weld at a higher frequency. Meaning that it helps to focus the TIG welding arc. It pinpoints the heat and allows for more precision.
A/C Balance
Adjusting the balance is very important for aluminum welding. Welders have to balance out between cleaning and penetration levels of the aluminum. The more balance you have the more penetration you will be able to achieve. Settings usually vary from 70% to 80% for this type of welding.
Pre Flow and Post Flow Time
Pre flow is the time the gas flows from the torch before getting an arc. One shouldn’t go beyond 0.5 or ½ of a second. Post flow is the time gas flows from the torch after the arc stops.
How to TIG Weld
Before getting down and messy and actually doing some welding work, a welder has to prepare properly. This means making sure that the metal joint is ready and that your working area is set up properly. One also needs to take into account preparations associated with arc welding different types of metal.
But before you start any kind of work, make sure that you have your protective gear on. The safety gear includes a welding helmet, coverall, and leather gloves and shoes.
Sometimes the angle, size or a look of the weld is specified on the welding drawings by a specific welding symbol. For welders, understanding the symbols is as important as learning how to weld.
Prepare Metal Joint and Welding Table
Joint preparation is an important aspect of welding TIG. The joint has to be completely clean and the welder needs to make sure that there is no rust, paint, oil, nor oxidation before one starts their work. The joint must be cleaned with either a grinder or, in the case of aluminum, a chemical cleaner.
As far as the welding table goes, a bit of metal area is needed in order for electricity to go through your metal. A welding table is the best choice but a big piece of sheet metal can also do nicely.
Also, you need to make sure to attach the ground cable with a clamp to the workpiece you plan to weld. It is also advisable to spray your welding table with an anti-spatter in order to prevent any leaking metal from sticking to the table.
TIG Welding Stainless Steel and Steel
TIG welding steel and stainless steel are similar. You still need the same Tungsten electrode and Argon gas flow for both types of metal. But the main difference is that when you weld stainless steel you need immense gas coverage and should increase the gas flow.
In certain situations, you will need to completely submerge the weld with Argon gas. Also, if you are working on an open root weld, you will need to purge the inside of the joint with a filler gas.
TIG welding stainless steel may cause it to warp if too much heat is applied. But by bracing the weld area frequently one can avoid distortion from happening. If you have done things correctly, the weld should have a copper color. But if it is grey or darker it means that you applied to much heat or you have been moving slow.
We made a full article about welding stainless steel and its alloys and if you want to check that out it’s here.
TIG Welding Aluminum
TIG welding is commonly associated with welding aluminum. But that said, not every TIG welder can properly weld aluminum. Especially when we are talking about thin gauge aluminum.
The most important thing when TIG welding aluminum to set up is the Tungsten electrode. To weld it, you either need pure Tungsten or Zirconium Tungsten. The 2% lanthanated Tungsten is probably the best choice as it can hold up at higher amperages. The Tungsten should also have a ball-shaped head in order to properly spread heat.
The current type of aluminum welding should always be AC welding. D/C TIG aluminum welding is possible with a DCEN setting and pure helium. However, it takes advanced knowledge to do it and welders usually don’t do this. For this to work, the aluminum needs to be incredibly clear. Also, the reason for doing it is when welding a very thick type of aluminum.
Lastly, cleaning the area that you are about to weld is important. If you want the highest quality of the aluminum weld you need to make sure that everything is pristine before you start your work. You can clean the oxide layer with a stainless steel wire brush or a carbide cutter.
Adjust the Balance Control
Adjusting proper balance control is another key element for making a proper aluminum weld. When welding in A/C polarity, the electrode has an electroide-negative (EN) cycle and a portion of an electrode-positive (EP) cycle. The EN is the welding side while the EP is needed for cleaning and removing oxide.
Using modern welding machines, the balance control feature allows you to adjust between the two while working in response to the weld puddle.
Why is Aluminum so Difficult to Weld?
There are certain properties that aluminum has that make it extremely hard for TIG welding.
First of all, aluminum has a melting point of 1,200 F (640 C) and does not change color before it starts to melt like other metals. The melting point of the oxide skin that forms on the surface is 3,200 F (1,700 C). Additionally, aluminum boils at a lower temperature (2880 F or 1,580 C) than the oxide melts. The oxide is also heavier than molten aluminum and can sink and get trapped in it. You can see how important preparation is and why one needs to remove the oxide skin properly.
You can see why a TIG welder may have so much trouble when working on aluminum.
Frequently Asked Questions [FAQ]
Is It Hard To TIG Weld?
Although considered as one of the more difficult welding processes, to pick up, TIG welding can still be learned with enough practice. Some would say that it is a lot easier than MIG welding and stick welding, but it all depends from person to person. All in all, with enough dedication and work one, can easily understand how to do it.
Can You Teach Yourself To TIG Weld?
TIG welding is a very clean and versatile welding process. As opposed to MIG welding, for instance, it requires being able to understand various concepts before starting to do it. Thus if you are able to learn everything about it, people can learn it by themselves with a lot of work.
Can You TIG Weld Anything?
Basically yes! TIG welding allows you to weld almost any type of material, more types than MIG welding. You can weld copper, titanium, aluminum, steel, stainless steel, magnesium and many more types of metal.
Finishing Up
There you have it! This is everything you need to know to become a successful TIG welder. Mind you, it is not as easy to learn as one may think and it does take years of practice to acquire this craft.
But once you manage to understand all the fundamentals about it, TIG welding becomes immensely easier. Additionally, it allows you to become a more versatile welder by enabling you to weld under different circumstances and a wider variety of materials.
We have recently covered an innovative approach to TIG welding called TIP TIG welding, in our latest article. While expensive for beginners, it’s definitely interesting to learn about. The TIP TIG doesn’t have the disadvantages of traditional TIG like the need for high expertise or the slow welding speed, making it one of the best welding processes overall.
Resources:
- How a TIG Welder Works and When to TIG Weld at www.millerwelds.com
- Tig Welding Aluminum at www.weldingtipsandtricks.com by Jody Collier
- TIG Welding Aluminum using DC Electrode Negative and helium at www.weldingtipsandtricks.com by Jody Collier
- A basic understanding of tig welding, how tig welding works at www.everlastgenerators.com
- TIG welding tips at bae.ucdavis.edu by Tom Bell
- How to “Correctly” Grind, Cut & Prepare Tungsten Welding Electrodes by www.diamondground.co.uk
- Guidelines for tungsten electrodes at www.thefabricator.com by Mike Sammons
- TIG Welding: What is Scratch-Start, Lift-Arc and HF Ignition at www.weldclass.com.au
- TIG Welding Aluminum at www.lincolnelectric.com