Welding is a lot more complex than it appears at times. One of the real areas of confusion for many people, when they first take up welding, is what kind of gas should you use?
There are 10 basic gases that are used in welding and they can be mixed together to create even more options!
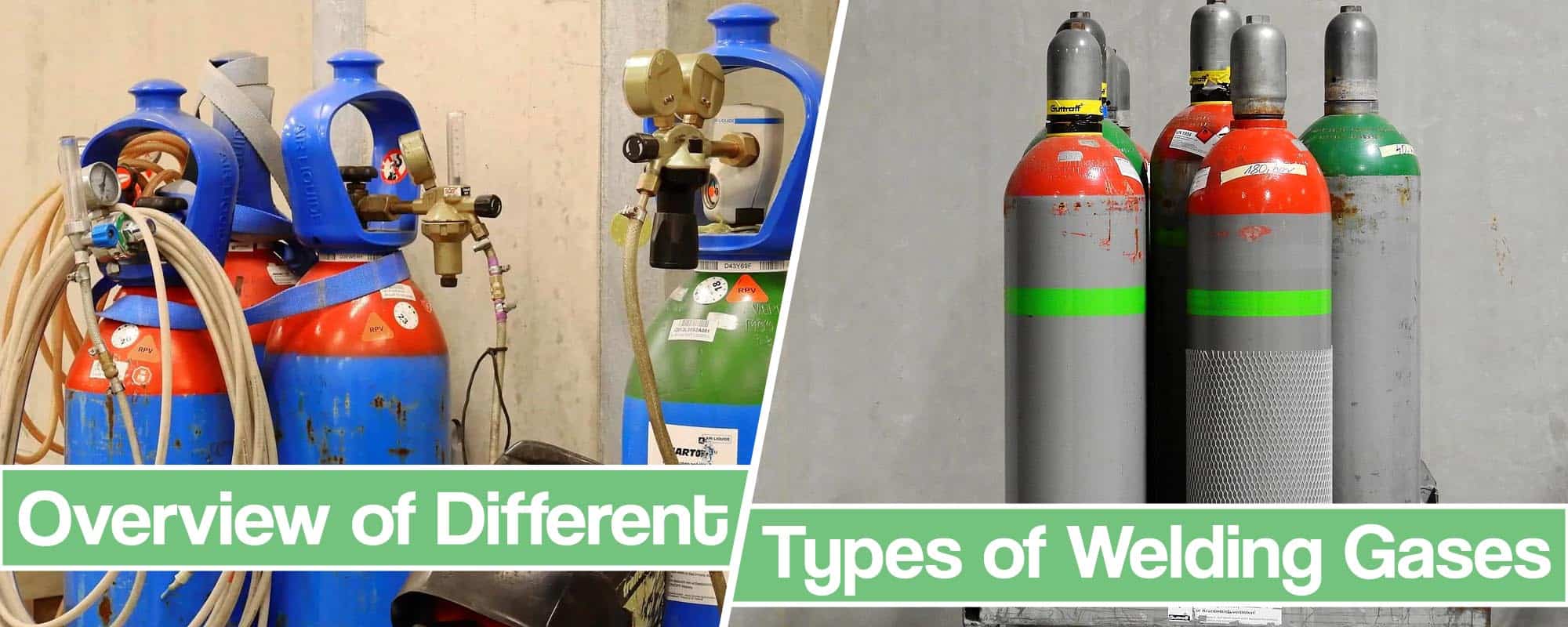
The good news is, however, that you can learn to quickly choose between them to get the job you want to be done, done well.
Our guide to the different types of gases available should reduce any confusion you have and make sure that every time you weld, you choose the right gas for your work and you do so with confidence!
Also, you can check our reviews of the best welding gas regulators
Inert and Reactive Gases In Welding: A Brief Overview
There are two types of gas that is applicable to welding:
- Inert gases. Inert means “nonreactive under a specific set of conditions”. This includes but is not limited to the noble gases (which are generally nonreactive in most conditions). Noble gases are also elemental (pure elements) but other inert gases are usually compounds.
However, it’s important to remember that all inert gases can be made to react given specific conditions and this is why choosing your gas for welding is an important step.
- Reactive gases. As the name suggests these gases are chosen for their ability to react with other elements or compounds. They can create changes in the state of the weld or the welding conditions.
What Is Gas Used For In Welding?
There is a range of different uses for gas in welding. This can include: keep the arc clear of impurities (such as dust, other gases, dirt, etc.),
Also used for assisting arc stability and ensuring proper metal transfer for many welding processes. making sure that the welding pool stays clean below the seam (this is known as purging), for blanketing and for heating too.
If you don’t use gas properly in welding you can end up with a weak or porous weld or find that there is too much spatter while welding. Spatter won’t ruin the weld but it does reduce productivity as it requires effort to clean it up.
If you want to read about the hazards that welding fumes and welding gases pose, check this article.
Shielding Gas
Air that gets into the arc will form air bubbles in the molten metal. This makes the weld weak and unattractive. When you MIG or TIG weld, you have to use a shielding gas except in the case where the filler material is “flux-coated” or “flux-cored”.
In general, shielding gases will be inert. This is because they won’t react during the welding process and won’t change the stability or structure of the intended weld.
The choice of inert gas will affect the way the weld works and can improve penetration, change the fluidity of the metal when it melts and ensure the bead has a smooth surface.
Purging Gas
A purging gas does the same job as a shielding gas but on the underside of the weld.
This is typically done during stainless steel welding and it’s done by sealing the bottom of the joint and blowing gas over it (you can use the same or a different gas as that being used on the other side of the joint).
Blanketing Gas
Blanketing isn’t common but it’s done when you want to ensure that a weld won’t be stained or contaminated after the weld is finished. The space around the weld is filled with gas to drive out any airborne contaminants.
Sometimes this will involve placing the finished item in a tank of gas and other times by driving gas out of the existing space and replacing it with an inert gas.
Heating Gas
There is a type of welding such as gas welding and brazing that use the gas passed through the gun to increase the heat of the reaction on the filler rod. This, of course, requires a reactive gas.
There is no need for an arc when the gas is supplying heating power.
In many cases, heating via gas is a pre-heating process for a regular welding job.
The Different Type Of Gas Used For Welding
There are 10 different “pure” gases that can be used in welding. They are:
Argon (Ar)
Used in many welding processes, from the inert noble gases. Argon will not react with most other substances (though it will at extremely high temperatures). As the 3rd most common of the gases on Earth – it’s also a very cheap choice to use (in the US).
It’s a shielding gas used when working on stainless steel, aluminum, and titanium. It cannot be used in pure form for ordinary carbon steel because the arc will not be stable enough. Argon and CO2 mixture on the other hand provide the necessary arc stability for welding mild steel.
Argon welding gas is mainly used for shielding and in particular to keep contaminants in the air at bay.
It can be brought to bear in the primary welding stage or it can be used to purge the underside of the joint. It’s a sure choice for a MIG welding gas and the number one choice for TIG welding.
An Argon cylinder is a staple of most welding areas as argon welding is very common, indeed.
Carbon Dioxide or CO2
Also known as MIG gas Another very common option among natural gases (we exhale CO2 as do all animals – though plants inhale it). It is cheap and easy to produce on an industrial scale. CO2 welding gas (mostly used gas for MIG welding) is used for shielding the arc and molten pool.
CO2 costs even less than Argon does but there is a distinct reduction on the quality of the weld when compared with Argon and it can lead to more spatter than Argon too.
So, it’s more often used in a mix with something else than as pure CO2. Argon CO2 blends are very common.
If you want to read about MIG welding with pure CO2 check this article
Oxygen (O2)
We breathe Oxygen and it’s fairly important to all other life on Earth. It tastes of nothing, smells of nothing and is very reactive. To use Oxygen in welding, it’s normally mixed with other shielding gases to change the fluidity of the molten metal and it can speed things up too.
You can also use it to add heat when welding. If you mix it with acetylene, you can create a flame that will be enough to weld steel (the only flame that will).
Oxygen can also prevent the need for a “shielding flux filler wire” in your welding.
Helium (He)
Helium has a unique property that it doesn’t freeze – you can get a liquid state but not a solid one. It also makes you talk funny if you inhale it, which is where most of us encounter it.
There’s not much Helium on Earth and it’s hard to produce, so, it’s quite expensive when compared to other choices of welding gasses. It is used for shielding both by itself and in blends as it can help offer deep penetration and boosts the heat input but it can be hard to get a consistent arc start with it.
It works best when blended with Argon which compensates for the inconsistent starting properties of Helium. This kind of blend is used when welding nickel alloys for example.
Nitrogen (N)
The most abundant natural gas and makes up the majority of our atmosphere. Nitrogen can be used in shielding (for plasma cutting or laser welding).
It can be mixed to form blends with other shielding gases and that allows for some specialist usage, this gas won’t work with carbon steel but can work very well with nitrogen-rich metals.
It’s also a good choice when you want to do blanketing as it is very cheap and can be used in large spaces without worrying about the cost impact.
Hydrogen (H)
Hydrogen is a very reactive and simple element and yet, despite that, it’s mainly used as a shielding gas in welding. It’s used in blends in very small percentages and this is very safe and it can help increase the heat of the blend, It’s also used in a process called “atomic hydrogen welding”.
This requires pure hydrogen and it creates an incredible heat of up to 7200° F which helps weld metals with incredibly high melting points. It’s worth noting that atomic hydrogen welding is very dangerous and you would need very specialist training to do it.
The three gases below acetylene, propane, and propylene are used in oxy-fuel welding and are extremely flammable.
Acetylene
Acetylene is very flammable and it is highly combustible in the air. It is very easy to make and fairly cheap to use.
It’s combined with oxygen and used as a fuel source in certain types of welding. It produces a very hot flame that is capable of cutting or welding the majority of metals.
Propane
Propane is also very flammable and it is highly combustible in the air. It is better known as LPG (Liquid Petroleum Gas) and is used as a fuel source in many contexts.
It will burn the skin if it comes into contact with it. Surprisingly, however, it cannot be used in gas welding because unlike acetylene when you burn it in oxygen it does not create a reducing zone (that would clean the steel surface as you weld).
It is used mainly for brazing after welding is finished.
Propylene
Propylene isn’t actually a pure gas, it’s a blend with Oxygen. It will burn at a much higher heat than Propane and Oxygen will and it’s completely suited for non-structural fusion welding, brazing, heating, and more.
However, it’s generally supplied in small, disposable canisters that aren’t really big enough to enable heating during welding of large items.
Compressed Air
As you might expect compressed air is the cheapest of the gases that are used in welding because it’s air. (Though it is often purified a little). When you mix compressed air with another fuel then it can produce a strong flame at a lower temperate than an oxy-fueled flame. For welders, this means that they can get greater control over the thickness of carbon coating they apply to the weld.
The Different Type Of Mixed Gases Used In Welding
Argon & CO2
The most common mixed gas for shielding in welding is a CO2 Argon Mix. It can run from 95% – 80% Argon and 5% – 20% CO2. In most applications, this will create a pleasantly smooth weld and keep the amount of spatter to a minimum.
The thicker the steel you’re looking to weld, the more Carbon Dioxide you require in the mix and the thinner it is, the more Argon you need. This is also one of the main mixtures used as MIG welding gas, and more about that you can read In this article
Argon, CO2, & Oxygen
If you’re looking for a little more fluidity in the weld pool then you’re probably looking for an Argon, CO2 gas & Oxygen mix. You get fairly similar properties to the Argon, Carbon Dioxide blend when it comes to the finished weld.
However, in addition to the improved fluidity, it can also improve the travel speed of the welding process and make a welder much more productive.
Argon, Helium, CO2
There is a wide range of different mixes available when your chosen weld gas is an Argon, Helium, Carbon Dioxide mix. Depending on what it will be used for the mix will either be dominated by Helium or Argon.
The gases used, make this mix suitable for welding anything from carbon steel to stainless steel, and it can even be used as an aluminum welding gas. (a good mixture for welding stainless steel with MIG machines)
Helium & Argon
If you’re looking for gas for welding Aluminum then you’re probably going to go with Helium & Argon mixed together. In addition to Aluminum, it’s also suitable for welding alloys.
Why? Well because the mix provides a deeper level of penetration and also delivers a wide-finish on the weld itself.
Argon & Oxygen (o2)
This mix of gases isn’t suited to stainless steel and if you are welding steel with it – it will normally be light gauge steel. Its purpose is to help with the material fusion of the steel.
You won’t normally find very much Oxygen in this argon gas mix because otherwise, it would burn too hot and argon gas welding is for finer things and thinner materials.
Argon & Hydrogen
If you’re TIG welding with gas then a mixture of Hydrogen and Argon is ideal when you need a clean weld. The hydrogen prevents any oxygen in the air from getting into the weld and causing oxidation.
The waste product of this reaction is water which quickly evaporates under the heat of welding.
Nitrogen & Hydrogen
This mix has a fairly specialist use and it’s a shielding gas for the preparation of austenitic (that is high in chromium and nickel with low carbon) stainless steels.
It enables a higher level of penetration whilst making the welding process go faster. It also helps to improve the mechanical properties of the stainless steel end product.
Laser Gases In Welding
As you might expect the laser processing industry has fairly exacting standards for laser gases – they can contain helium, nitrogen, CO2, and even CO (Carbon Monoxide).
Their primary purpose is to keep contaminants out of the laser system which can reduce the power of the laser and dramatically increase costs via damage to the optics and the costs of repair thanks to downtime.
Gas Supply Systems
The supply systems that are used for shielding gases can have an impact on the quality of the gas.
Pure Gas Supply
Compressed-Gas Cylinders
These cylinders require a regular refill and thus are the easiest to contaminate. Sometimes they will have a built-in purity check on the valve (this requires a cylinder valve). Some grades are available for purchase with a full analysis of impurities supplied with them.
Liquid Cylinders
You tend to get a better level of quality control with liquid cylinders (sometimes called VGLs or dewars too). You may be able to get an analysis of impurities supplied at the point of purchase as well.
Bulk Liquid Gases
You would expect a high level of purity in this gas as it is transferred directly from production to your on-site storage.
Tube Storage Systems
These are trailer mounted (but occasionally may be skid or ground-mounted) and like compressed cylinders are regularly refilled which can introduce impurities.
Mixed Gas Supply
Many of the most common shielding gases are supplied in cylinders or from a variety of other storage systems. Much of this will be based on the quality required and the quantity required.
The use of switchover manifolds when using cylinders or packs of compressed shielding gases can keep contamination to a minimum.
Piping
The quality of the pipe that moves gas from its supply point to your gas metal arc is also vital. The weld pool can be contaminated very easily in some metal arc welding situations. Welded stainless steel makes for the best piping in these situations.
About Gas Safety
The majority of gases used in welding are not flammable but that doesn’t mean they can be treated carelessly. A flammable gas, such as acetylene, however, must be treated with additional care.
The only time that a flammable gas should be in the same area as a welding machine is when it’s in use. You must have a Class B fire extinguisher on hand when metal arc welding with flammable gasses. (If you can’t find a label CO2 or dry powder are acceptable but not water).
You can’t set fire to inert gas. You can, however, suffocate on it if you allow it to fill the space that you’re in. If you’re arc welding in conditions with poor ventilation, you must ensure that you have proper protective processes in place to work.
That means extractor fans, gas detectors, a spotter and you should also ensure you take regular breaks to reduce the overall danger of inhalation problems.
Always make sure your gas tank is in good condition, while accidents are rare – if the valve sheers off at the top of the tank – the whole thing will fly around the room in a very dangerous fashion. This is especially important when using gas MIG welder, they have a lot of little parts and valves that can leak and make problems for you.
Frequently Asked Questions (FAQs)
What Happens If You Weld Without Shielding Gas?
The weld will become porous and weak. You should never weld without a shielding gas unless you are work with flux-clad or flux-core arc welding material. The molten weld pool and the weld will get contaminated by the absorption of nitrogen, oxygen, and hydrogen from the atmosphere.
Which Welding Gases Are Inert?
Argon and Helium are both inert and CO2 and Nitrogen are often considered to be semi-inert MIG welding gases.
Which Gas Is Used In Welding?
There are 10 different gases including Argon, CO2, Oxygen, Helium, Nitrogen, Hydrogen, Acetylene, Propane, Propylene and Compressed Air. These may also be found in different mixes to create different arc welding outcomes.
What Is The Most Common Gas Used In Welding?
The most common gas for welders is an Argon and CO2 mix because it is low cost and gives good results under most conditions.
What Is A Shielding Gas In Welding?
Argon and CO2 (mostly used in with MIG welder. You can hear people call them gas MIG welders because of that) are the most common shielding gases in welding but other gases can be used in some circumstances. Even Oxygen can be added to a mix of gases to become a shielding gas for gas metal arc welding (but this is rarely).
Which Gas Is Best For MIG Welding?
Argon is considered to be the best gas for gas metal arc welding. It can be used for welding all grades. It is, however, often mixed with other gas to refine the results that it gives including CO2, Helium, and even Oxygen.
Conclusion
As you can see, there’s a lot of choices when it comes to gases and there are a surprising number of different uses for them when it comes to the work you want to do.
However, it’s not normally that difficult to work out what gas is right for the job in hand. With the exception of some of the more specialist applications of welding, you should be able to narrow down your options pretty quickly.
We hope that our guide to the different types of welding gas has helped you get to grips with this important subject. And if you are interested in my reviews of the best multi-process welders you can check the page here.
Resources:
- Effects of Shielding Gases in GMAW
- Noble gas by Gary J. Schrobilgen at Encyclopædia Britannica
- Gas Welding Safety at nasdonline.org
- Controlling Hazardous Fume and Gases during Welding OSHA.GOV
- MIG Welding Shielding Gas Basics at www.bernardwelds.com
- What Are Welding Shielding Gases, And Why Are They Important? by Oanh Nguyen at weldingschool.com