Now bear in mind that to learn this awesome welding trade you will need to finish welding school or a welding course and you will need a lot of practice – you can’t get that knowledge reading blogs on the internet.
What you can get here and what we will write about is some basics and some “have to know” tips about welding. Theoretical knowledge about welding processes and how they differ from one another.
Welding positions, and what are different welding gases and what current is used for what material.
There are also ( and there will be more) other articles about interesting subjects that are related to the welding trade that you should probably know and have in your head if you are planning to be a welder.
We hope that you will appreciate our writing.
START HERE:
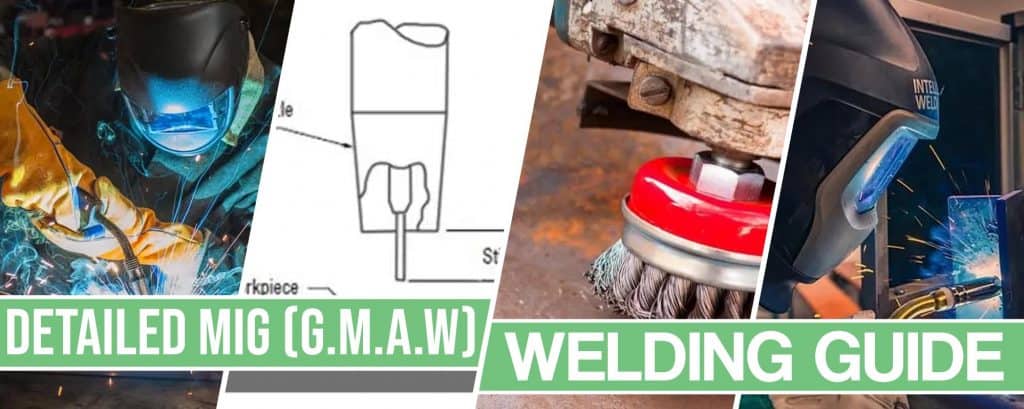
How to MIG Weld
This is a foolproof beginner's guide on how to MIG weld. We covered everything you should know from cleaning the metal to setting up a machine, things like wire speed, amperage and ultimately how to lay your first beads. Almost everyone starts with MIG so and this article will teach you everything you should know.
Welding Aluminum Explained in Detail
Welding aluminum is the advanced stuff. This is a very tricky metal to weld and there is a lot to know about doing it with different welding processes. In this article, you will learn why it is so difficult to do it properly, what processes can it be welded with and how to actually weld aluminum.
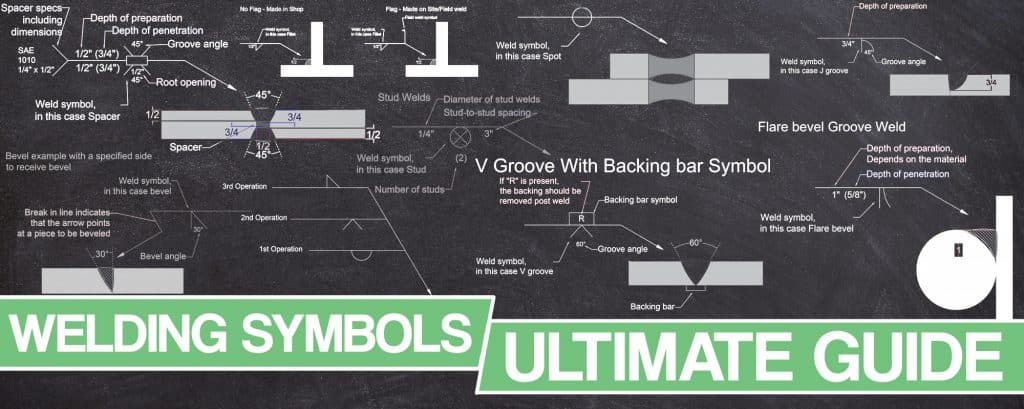
Welding Symbols Charts and PDF
Welding symbols are essential in a professional welding environment. You can't own a welding shop or work in any other environment like fabrication without knowing what kind of a weld you are making. In this article, you will learn everything about every welding symbol and you can download our free PDF book about them.
WELDING KNOWLEDGE AND EXPERIENCE:
Don't expect that you will learn to be a professional welder from the internet alone.
Reading articles on the web is a great way to stay informed, learn new things in theory and find out what is it that you don't know yet. However, if you actually want to learn, you will need to practice, fail, repeat until success. Things like welding aluminum take years to master so don't get discouraged if it doesn't work out from the first try. Start with the basics and build up from there.
Additionally, if you want to be a real professional you will have to know theory as well. That's why welding schools are important. Especially if you wish to go next level and be an instructor or a welding inspector.
Never underestimate the dangers of welding. Never stop learning about welding safety. Welding fumes, arc radiation, physical injuries, electrical shocks and others are always lurking as a hazard as you are welding. A big part of your welding knowledge should revolve around doing things properly, up to the safety standards and never jeopardizing you or those around you as you weld.